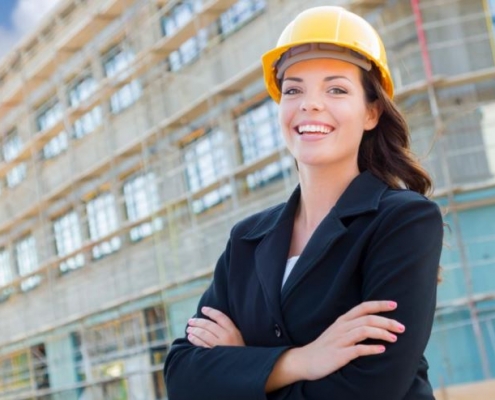
How Much Do Construction Workers Make? Surprising Stats in 2025
0 Comments
/
In today's bustling construction industry, one question often…
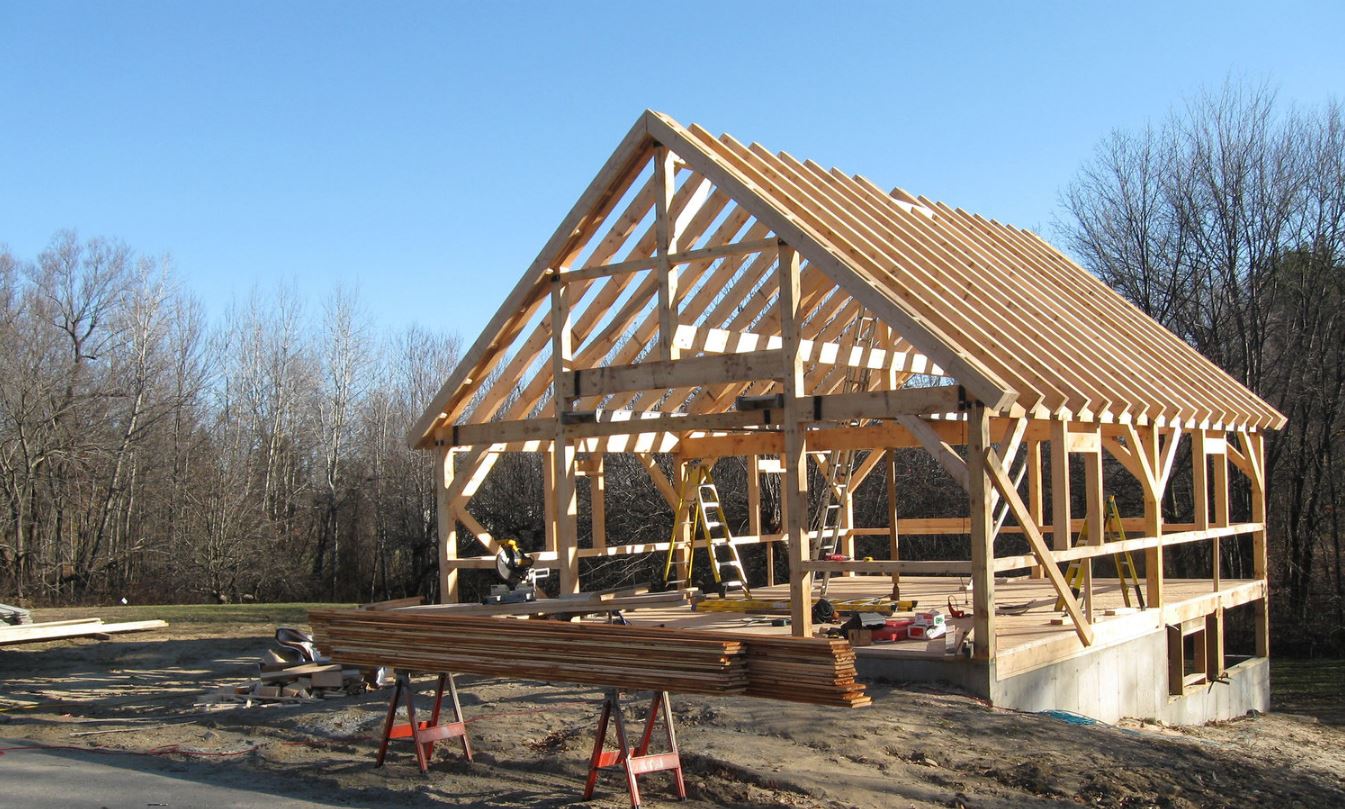
Basement Finishing: Turning Unused Space into Valuable Living Areas
Unlocking Your Home’s Hidden Potential with Basement Finishing
Basement…
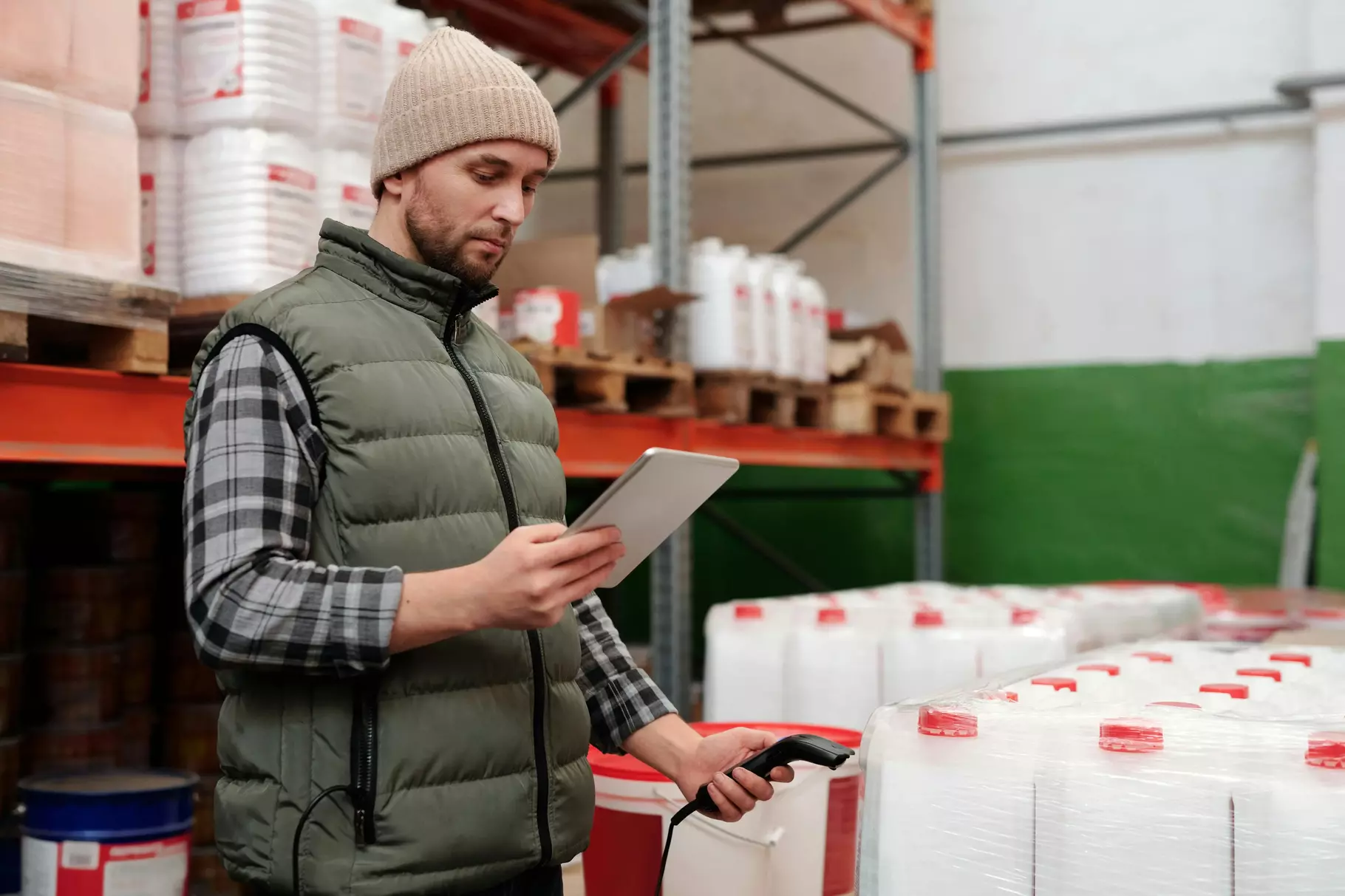
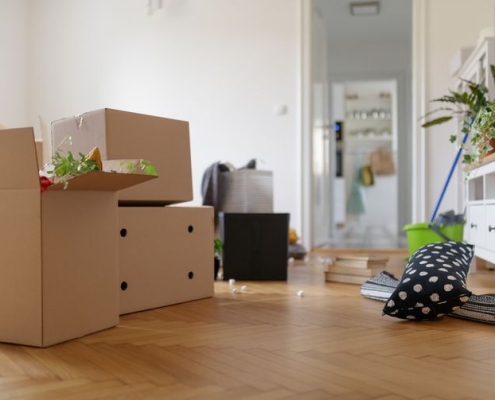
Commercial & Residential Construction Services in Irvine - Guide
Irvine, California, known for its planned urban development and…
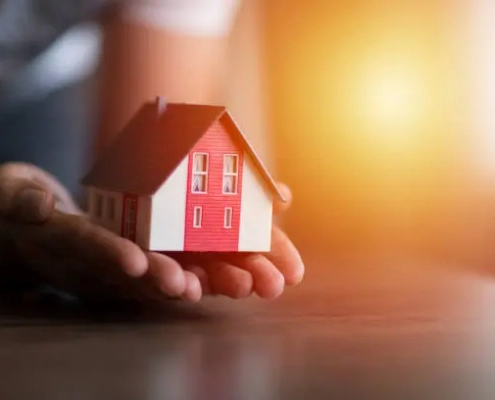
Residential Construction Services in Irvine
Irvine, California, is a city known for its beautiful homes and…
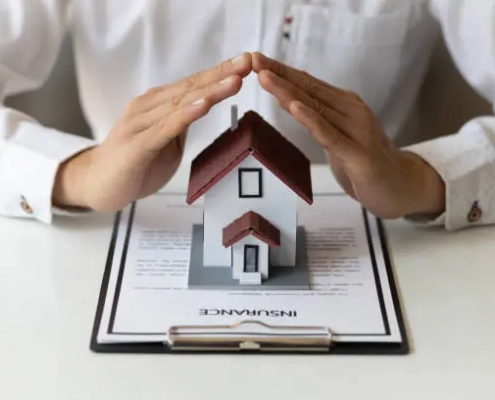
Residential Construction Services in Irvine
Irvine, a city in California, is known for its beautiful homes…
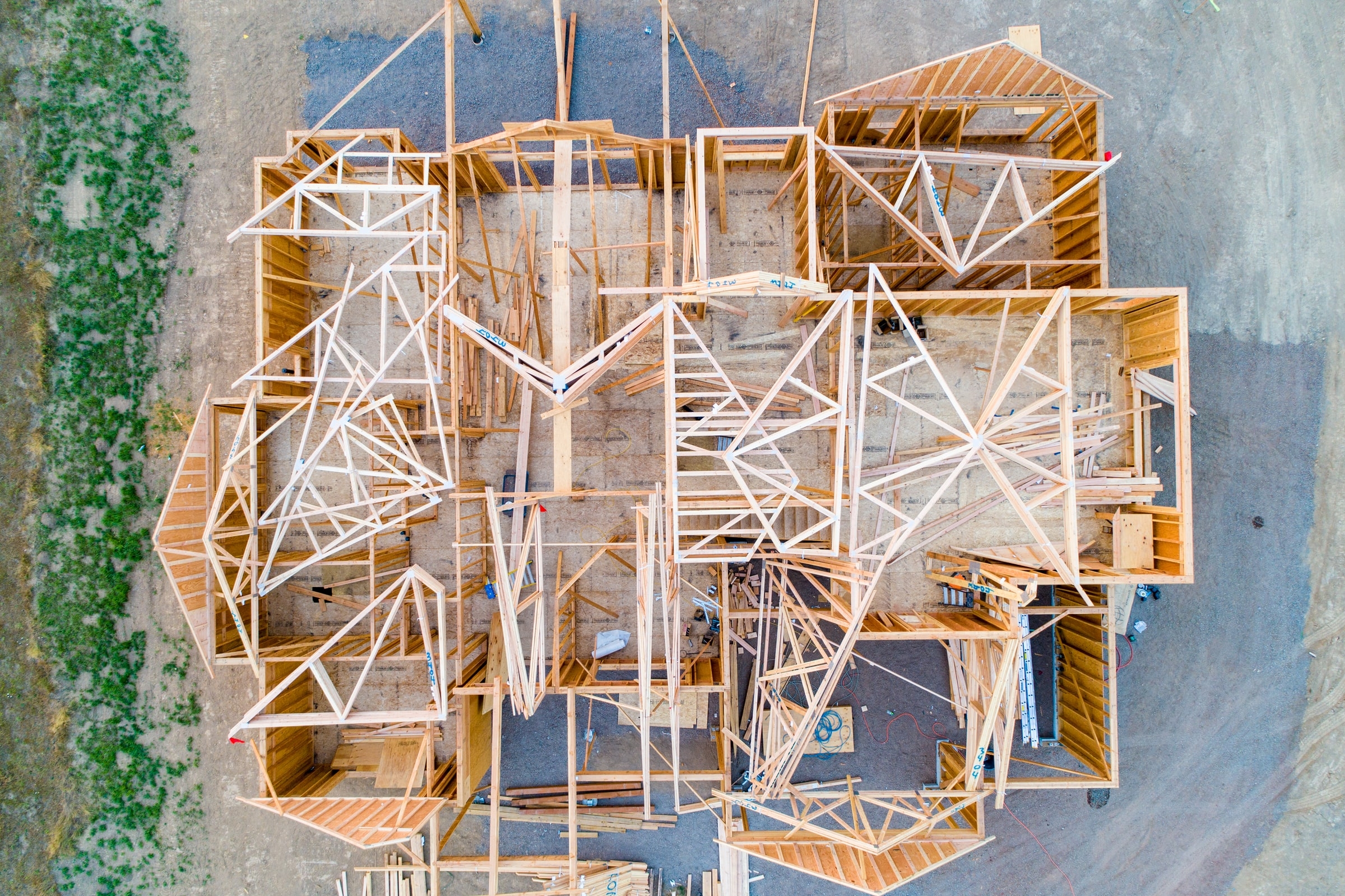
How To Calculate Price Per Square Foot New House Construction?
New house construction is a major undertaking. You need to be…

What Is Balloon Frame Construction?
The Balloon frame was a popular form of timber structure used…
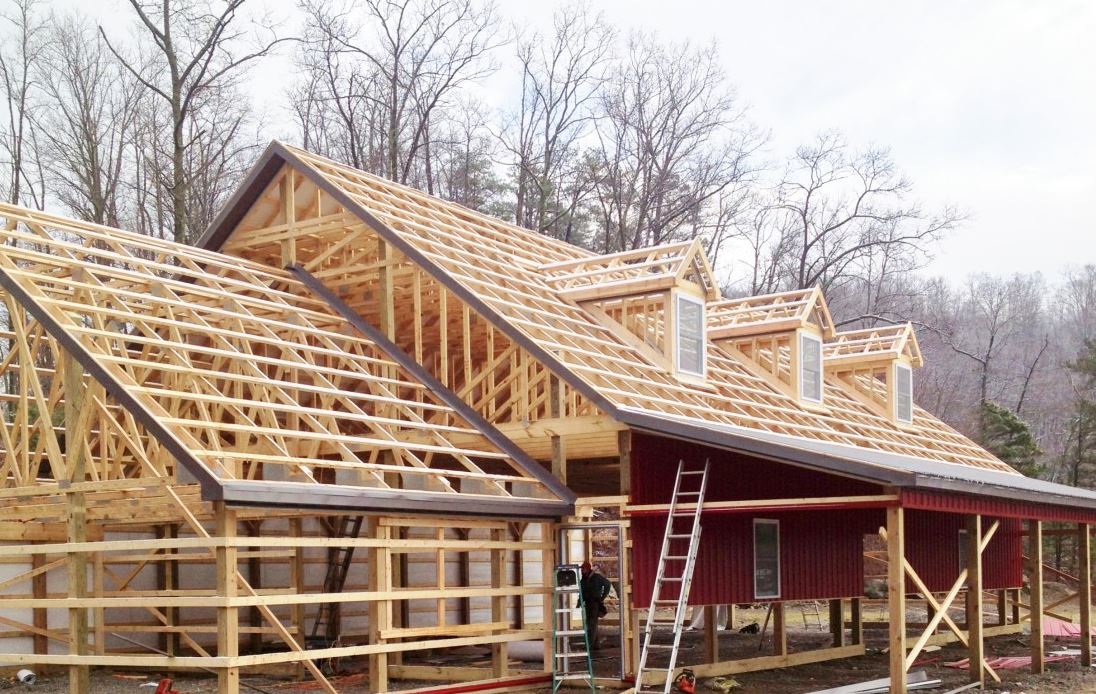
What Is Post Frame Construction?
Post Frame Construction is a wooden frame system fabricated with…